The heart of computational materials science and engineering lies in providing fundamental insights and understanding of materials behavior and properties across different scales, which further enables cost-effective design of materials with targeted properties. The significance of this topic area is highlighted by the Materials Genome Initiative (MGI) and the integrated computational materials engineering (ICME) paradigm where the central theme is inverse materials design by elucidating the link between processing, structure, properties and performance (aka PSPP links). Built on the PSPP links, our research covers three major components of design methods for emerging materials, i.e., representation, evaluation, and synthesis. For design of heterogeneous microstructural systems, we develop statistical frameworks and tools that are tailored to a wide range of material systems. Advanced machine learning (e.g., Gaussian random process and deep learning), Bayesian inference, dimension reduction, and many more techniques are employed to address challenges such as high dimensionality, lack of data, big data, mixed-variable metamodeling and optimization. For design of metamaterial systems, topology optimization and generative methods have been examined for designing multiscale and multifunctional structures. Our methods enable the integration of analyses and design decisions over multiple domains across manufacturing, structural mechanics, and design optimization.
The heart of computational materials science and engineering lies in providing fundamental insights and understanding of materials behavior and properties across different scales, which further enables cost-effective design of materials with targeted properties. The significance of this topic area is highlighted by the Materials Genome Initiative (MGI) and the integrated computational materials engineering (ICME) paradigm where the central theme is inverse materials design by elucidating the link between processing, structure, properties and performance (aka PSPP links). Built on the PSPP links, our research covers three major components of design methods for emerging materials, i.e., representation, evaluation, and synthesis. For design of heterogeneous microstructural systems, we develop statistical frameworks and tools that are tailored to a wide range of material systems. Advanced machine learning (e.g., Gaussian random process and deep learning), Bayesian inference, dimension reduction, and many more techniques are employed to address challenges such as high dimensionality, lack of data, big data, mixed-variable metamodeling and optimization. For design of metamaterial systems, topology optimization and generative methods have been examined for designing multiscale and multifunctional structures. Our methods enable the integration of analyses and design decisions over multiple domains across manufacturing, structural mechanics, and design optimization.
Jump to
Microstructure Characterization & Reconstruction (MCR)
Computational microstructure characterization and reconstruction (MCR) consists of statistical methods to quantitatively represent the microstructure (characterization), and to build an ensemble of statistically equivalent microstructure samples (reconstruction). Following the paradigm of “microstructure mediated design”, we have developed a wide range of MCR methods – correlation functions, physical descriptors, spectral density function, supervised learning, and deep learning techniques (e.g., transfer learning and generative adversarial networks). Stochasticity is a key feature across all our MCR methods. Leveraging the capabilities of MCR, we have explored PSPP linkages in several diverse material systems such as nanodielectrics for energy storage, rubber-based nanocomposites for vehicle tires, quasi-random photonic structures for light trapping, bulk heterojunction active layer in organic photovoltaics, etc.
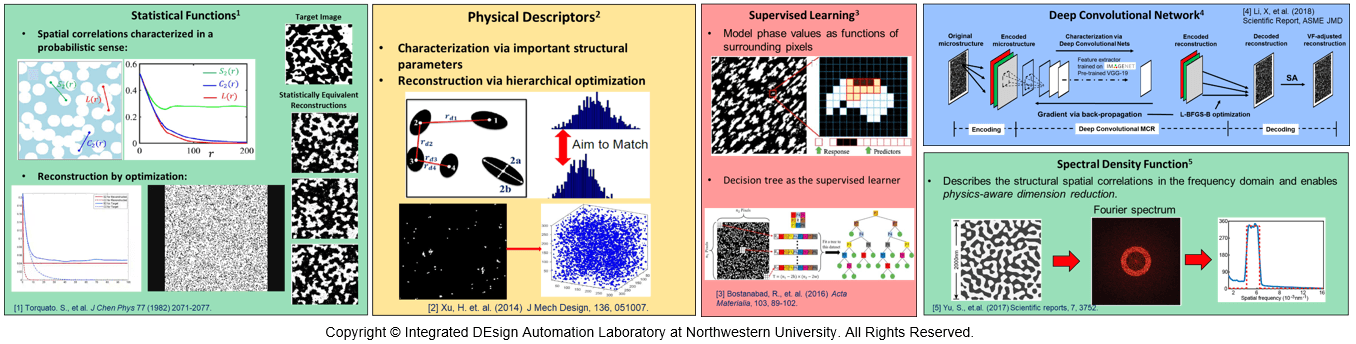
MCR Methods
Machine Learning of Materials Behavior
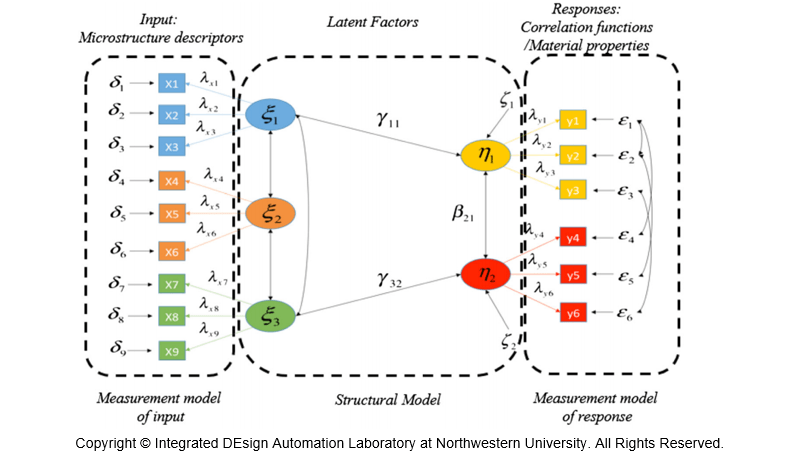
Structural Equation Modeling
Dealing with high dimensional data is one of the major challenges in establishing microstructural PSPP relations. We have employed machine learning techniques for “feature selection” to identify key microstructure features and “feature extraction” to reduce the dimensionality of microstructure representation. For descriptor-based microstructure representation, we have employed principal component analysis (PCA), relief algorithm, and structural equation modeling (SEM) for machine learning. In our recent development, we transferred the convolutional layers of deep neural networks used for MCR to structure-property prediction, and employed adversarial networks to identify latent variables for feature extraction. In lack of data, Gaussian random process models have been used as statistical inference models for capturing PSPP relations.
Multiscale Uncertainty Quantification in ICME
Uncertainty is inevitably introduced in materials’ behaviors starting from the design and constituent selection stages, through the manufacturing processes, and finally during operation. For this reason, ever-growing research is being conducted to rigorously couple computational models with statistical uncertainty quantification (UQ) and uncertainty propagation (UP) methods to provide probabilistic predictions that are in line with the observed stochasticity in materials. UQ and UP are actively pursued in various fields of science and engineering. They are, however, seldom applied to multiscale simulations due to the significant computational costs and complexities.
Our goal is to devise a non-intrusive UQ and UP approach that characterizes the uncertainties via random fields (RFs) and is applicable to multiscale simulations where multiple uncertainty sources (including spatial microstructural variations) arising from different length-scales are coupled and spatially dependent. We are focusing on developing non-intrusive approaches without changing the formulations of multiscale computer models.
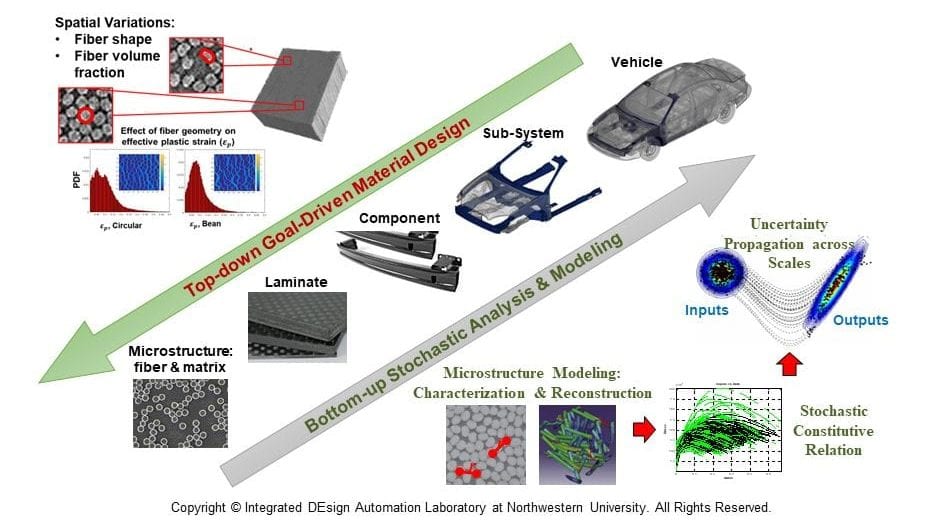
ICME Development of Carbon Fiber Reinforced Polymer Composites for Lightweight Vehicles
Data-driven Materials Design
To combat the experimental and computational costs of materials design, we are developing several data-driven methods. With parametric-based microstructure representations, e.g., the descriptor-based approach and the Spectral Density Function (SDF), we employ parametric optimization for microstructural design. Not only do those representations provide significant dimension reduction, they also offer physically meaningful PSPP mappings that are utilized to determine the optimal microstructure and improve manufacturability. Using deep learning methods such as Generative Adversarial Networks (GANs), we learn the complex morphological features and then leverage the latent variables to design the microstructure with the desired properties. For materials design with expensive computer simulations and the presence of both quantitative and qualitative design variables, we have developed a novel Latent Variable Gaussian Process (LVGP) approach that can be easily integrated with Bayesian Optimization, an effective data-driven design method, for adaptive global optimization.
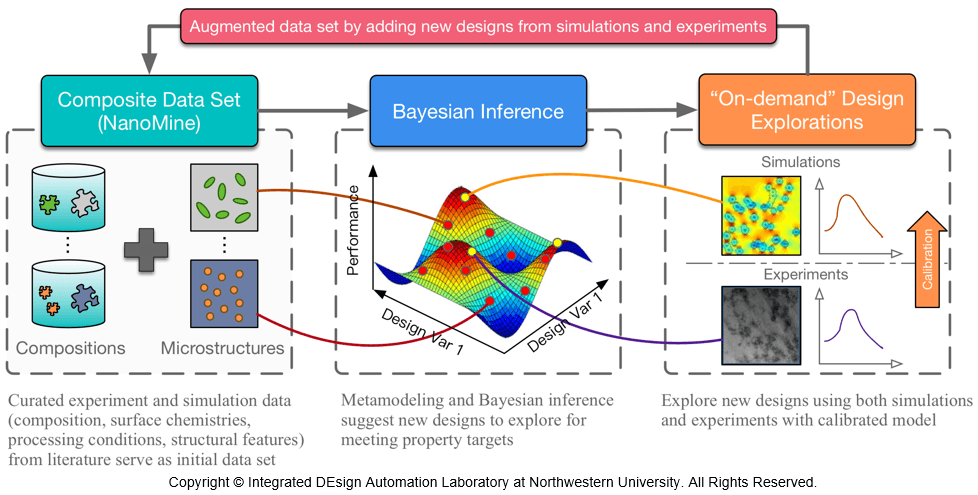
Data-driven Design Explorations
Topology Optimization and Metamaterials Design
By determining the optimal material layout, topology optimization (TO) creates non-intuitive structures with properties superior to their conventionally-designed counterparts. Bolstered by advancements in additive manufacturing, multi-material and multiscale methods have emerged as powerful design tools for metamaterials, which are composed of micro- or mesoscale unit cells. These unit cells are tiled throughout the macroscale structure, leading to extraordinary mechanical, optical or acoustic properties. We have developed density-based, level-set, and Connected Morphable Components (CMC) TO methods for discrete, continuum and multiscale structures. Moreover, our robust shape and topology optimization (RSTO) methods account for the uncertainty inherent in manufacturing and real-world applications, i.e., variations in geometry, material or mechanical properties due to imprecise processes and random loads. Our work also addresses the challenges facing the integration of design and manufacturing, such as exploiting high dimensional design freedom while ensuring the manufacturability and connectivity of the designs.
Design for Additive Manufacturing
Additive manufacturing (AM) offers unprecedented design freedom but its multi-physics and multiscale nature, combined with exorbitantly expensive experiments, make it extremely challenging to ensure consistent and high quality parts. Although recent progress in AM simulations bode well for virtual testing, the high-fidelity models are still too computationally intensive for the validation of a single part, let alone iterative design and optimization. Our goal is to create data-driven computational methods and tools that quickly predict the highly location- and path-dependent properties within AM-built parts, and that capture the uncertainty in the processing conditions and materials. In particular, we are developing methods for dimension reduction and rapid prediction of the spatiotemporal evolution of the complex microstructure arising from cycles of extreme heating and cooling. Ultimately, our goal is to harness these efficient predictive models in a framework that integrates AM process and product design, assuring robustness and reliability from design to deployment.
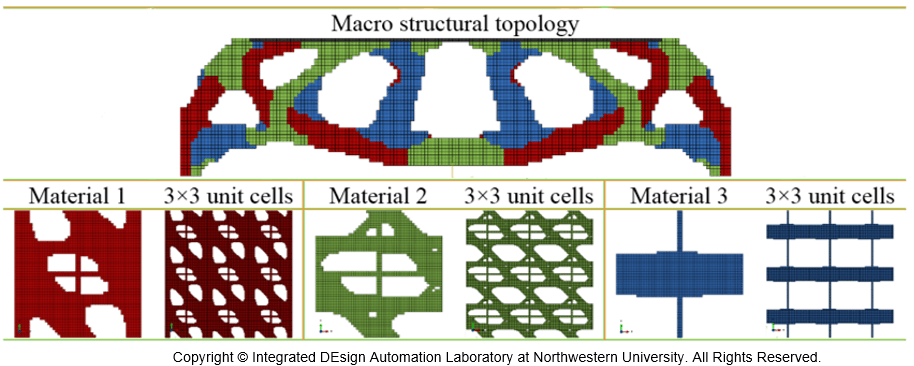
Multiscale Topology Optimization for AM
List of Publications
- Huang, T., Liu, Z., Wu, C-T., Chen, W., “Microstructure-guided Deep Material Network for Rapid Nonlinear Material Modeling and Uncertainty Quantification”, Computer Methods in Applied Mechanics and Engineering, 398, Article 115197, 2022.
- Ghumman, U.F., van Beek, A., Munshi, J., Chien, T., Balasubramanian, G., and Chen, W., “Designing Active Layer of Organic Solar Cells Using Multi-Fidelity Molecular Simulations and Spectral Density Function”, Computational Materials Science, accepted May 2022.
- Da, D. and Chen, W., “Simple Strategy towards Tailoring Fracture Properties of Brittle Architectured Materials”, International Journal for Numerical Methods in Engineering, in press.
- Iyer, A., Yerramilli, S., Rondinelli, J.M., Apley, D.W., and Chen, W, “Descriptor Aided Bayesian Optimization for Many-Level Qualitative Variables with Materials Design Applications”, Journal of Mechanical Design, special issue of IDETC 2022.
- Wang, L. Da, D., Chan Y.C., Liu, Z., Zhu, P., and Chen, W., “Generalized De-homogenization via Sawtooth-function-based Mapping and its Demonstration on Data-driven Frequency Response Optimization”, Computer Methods in Applied Mechanics and Engineering, 2022
- Tanriover, I., Lee, D., Chen, W., and Aydin, K., “Deep Generative Modeling and Inverse Design of Manufacturable Free-Form Dielectric Metasurfaces”, ACS Photonics, in press.
- Lee, D., Chan, Y-C, Chen, W.W., Wang, L., and Chen, W, “t-METASET: Tailoring Property Bias of Large-Scale Metamaterial Datasets through Active Learning”, Journal of Mechanical Design, special issue of IDETC 2022.
- Wang, L., Boddapati, J., Liu, K., Zhu, P., Daraio, C., and Chen, W., “Mechanical Cloak via Data-Driven Aperiodic Metamaterial Design”, Proceedings of National Academy of Sciences, 119(3), 2022.
- Chen, W., Iyer, A., and Bostanabad, R., “Data Centric Design: A New Approach to Design of Microstructural Material Systems”, Engineering, 2022.
- Wei, T., van Beek, A., Hao, J., Zhang, H., and Chen, W., “Bayesian Calibration of Performance Degradation in A Gas Turbine-Driven Compressor Unit for Prognosis Health Management”, Journal of Engineering for Gas Turbines and Power, 2022.
- Da, D., Chan Y.C., Wang, L, and Chen, W., “Data-driven and topological design of structural metamaterials for fracture resistance”, Extreme Mechanics Letters, 2022.
- Zhang, K., Apley, D. W., and Chen, W. “Nonstationarity Analysis of Materials Microstructures via Fisher Score Vectors”, Acta Materalia, 211,116818,2021.
- Lee, D., Jiang, S., Balogun, O., and Chen, W., “Dynamic Control of Plasmonic Localization by Inverse Optimization of Spatial Phase Modulation”, ACS Photonics, 2021.
- Giuntoli, A., Hansoge, N.K., van Beek, A., Chen, W., and Keten, S., “Systematic coarse-graining of epoxy resins with machine learning-informed energy renormalization”, NPJ Computational Materials, 7(1), 1-12., 2021.
- Dulal, R., Scougale, W, Chen, W., Balasubramanian, G., and Chien, T., “Direct Observations of Uniform Bulk-heterojunctions and the Energy Level Alignments in Non-Fullerene Organic Photovoltaic Active Layers”, ACS Applied Materials & Interfaces, 13(47), 56430-56437, 2021.
- Wang, L., van Beek, A., Da, D., Chan, Y-C., Zhu, P., and Chen, W., “Data-driven multiscale design of cellular composites with multiclass microstructures for natural frequency maximization”, Composite Structures, 2021.
- Munshi, J., Chen, W., Chien T-Y., and Galasubramanian G., “Towards improving the efficiency of organic solar cells by coarse-grained atomistic modeling of processing dependent morphologies”, Computing in Science and Engineering, 23(3), 48-55, 2021. DOI: 10.1109/MCSE.2021.3072626.
- Wang, L., Yerramilli, S., Iyer, A., Apley, D., Zhu, P., and Chen, W. “Scalable Gaussian Processes for Data-Driven Design Using Big Data With Categorical Factors”, Journal of Mechanical Design, 144(2), 021703, 2021.
- J. Munshi, W. Chen, T Chien and G. Balasubramanian, “Machine Learned Meta- Heuristic Optimization of the Bulk Heterojunction Morphology in P3HT:PCBM Thin Films”, Computational Materials Science, 187, 110119, 2021.
- Munshi, J., Chen, W., Chien T-Y., and Galasubramanian G., “Transfer Learned Designer Polymers For Organic Solar Cells”, Journal of Chemical Information and Modeling, 61, 134-142, 2021.
- Munshi, J., Chen, W., Chien T-Y., and Galasubramanian G., “Towards Improving the Efficiency of Organic Solar Cells by Coarse-Grained Atomistic Modeling of Processing Dependent Morphologies“, Computing in Science and Engineering, 23(3), 48-55, 2021. DOI: 10.1109/MCSE.2021.3072626.
- Munshi, J., Chen, W., Chien T-Y., and Galasubramanian G., “Transfer Learned Designer Polymers For Organic Solar Cells”, Journal of Chemical Information and Modeling, 61, 134-142, 2021
- J. Munshi, W. Chen, T Chien and G. Balasubramanian, “Machine Learned Meta- Heuristic Optimization of the Bulk Heterojunction Morphology in P3HT:PCBM Thin Films”, Computational Materials Science, 187, 110119, 2021
- Wang, L., Tao, S., Zhu, P., and Chen, W., “Data-Driven Topology Optimization with Multiclass Microstructures using Latent Variable Gaussian Process”, Journal of Mechanical Design, 143(3): 031708, DOI: 10.1115/1.4048628, Mar 2021.
- Chan, Y-C, Ahmed, F., Wang, L., and Chen, W., “Metaset: Exploring Shape and Property Spaces for Data-Driven Metamaterials Design”, Journal of Mechanical Design, 143(3): 031707, DOI: 10.1115/1.4048629, Mar 2021.
- Wang, Y., Iyer, A., Chen, W., and Rondinelli, J., “Featureless adaptive optimization accelerates functional electronic materials design”, Applied Physics Reviews, 7(4), 041403, 2020.
- Zhang, Y., Apley, D., and Chen, W., “Bayesian Optimization for Materials Design with Mixed Quantitative and Qualitative Variables”, Scientific Report, 10, Article number: 4924, 2020.
- Wang, L., Chan, Y-C, Ahmed, F., Liu, Z, Zhu, P., and Chen, W., “Deep Generative Modeling for Mechanistic-based Learning and Design of Metamaterial Systems”, Computational Methods in Applied Mechanics and Engineering, special issue on Artificial Intelligence, 372, 113377, 2020.
- Van Beek, A., Ghumman, U.F., Munshi, J., Tao, S., Chien T-Y., Galasubramanian G., Plumlee, M., Apley, D., and Chen, W., “Scalable Adaptive Batch Sampling in Simulation-Based Design with Heteroscedastic Noise”, Journal of Mechanical Design, 143(3): 031709, DOI: doi.org/10.1115/1.4049134, Mar 2021.
- Huang, T., Gao, J., Liu, Sun, Q., Su, X., Zeng, D., Liu, W-K., and Chen, W., “Stochastic Nonlinear Analysis of Unidirectional Fiber Composites using Image-based Microstructural Uncertainty Quantification”, Composite Structures, DOI: 10.1016/j.compstruct.2020.113470, accepted Dec., 2020.
- Brinson, L. C., Deagen, M., Chen, W., McCusker, J., McGuinness, D., Schadler, L., Palmeri, M., Ghumman, U., Lin, A., and Hu, B., “Polymer Nanocomposite Data: Curation, Frameworks, Access and Potential for Discovery and Design”, ACS Macro Letters, 9, 1085-1094, 2020, https://dx.doi.org/10.1021/acsmacrolett.0c00264.
- Munshi, J, Chien, T-Y., Chen, W., and Balasubramanian, G., “Elasto-morphology of P3HT:PCBM Bulk Heterojunction Organic Solar Cells”, Soft Matters, accepted June 2020. DOI: 10.1039/D0SM00849D, outside back cover article.
- Wang, C., Yu, S., Guo, X., Kearney, T., Guo, P., Chang, R., and Chen, J., Chen, W., and Sun, Cheng, “Maximizing Solar Energy Utilization through Multi-criteria Pareto Optimization of Energy Harvesting and Regulating Smart Window”, Cell Reports Physical Science, accepted June 2020, https://doi.org/10.1016/j.xcrp.2020.100108.
- Schadler, L.S., Chen, W., Brinson, L.C., Sundararaman, R., Gupta, P., Prabhune, Iyer, A., Wang, Y., Shandilya, A., “A Perspective on the Data-Driven Design of Polymer Nanodielectrics”, Journal of Physics D: Applied Physics, 2020.
- Wang, L., Chan, Y-C., Liu, Z., Zhu, P., and Chen, W., “Data-Driven Metamaterial Design with Laplace-Beltrami Spectrum as ‘Shape-DNA’”, Structural and Multidisciplinary Optimization, 61, pp. 2613–2628, DOI: 10.1007/s00158-020-02523-5, February 2020.
- Chen, G., Shen, Z., Iyer, A., Ghumman, U.F., Tang, S., Bi, J., Chen, W.*, and Li, Y.*, “Machine-Learning-Assisted de novo Design of Organic Molecules and Polymers: Opportunities and Challenges”, Polymers, 12(1), 163, https://doi.org/10.3390/polym12010163, 2020.
- Zhang, M., Li, X., Wang, Y., Chen, W., and Brinson, L.C., “Impact of Interfacial Properties on the Viscoelastic Relaxation of Hard-Soft Block Copolymers using Finite Element Analysis”, Journal of Polymer Science, Part B: Polymer Physics, July 2020. DOI: https://doi.org/10.1557/jmr.2020.161.
- Zhang, Y., Apley, D., and Chen, W., “Bayesian Optimization for Materials Design with Mixed Quantitative and Qualitative Variables”, Scientific Report, 10, Article number: 4924, 2020.
- Iyer, A., Zhang, Y., Dulal, R., Ghumman, U.F., Chien, T., Balasubramanian, G., and Chen, W., “Designing Anisotropic Microstructures with Spectral Density Function”, Computational Materials Science, 179, 2020.
- Munshi, J., Dulal, R., Chien, T., Chen, W., and Balasubramanian, G., “Solution Processing Dependent Bulk Heterojunction Nanomorphology of P3HT/PCBM Thin Films”, ACS Applied Materials & Interfaces, 11 (18), 17056, 2019, https://doi.org/10.1021/acsami.9b02719.
- Mozaffar, M., Bostanabad, R., Chen, W., Ehmann, K., Cao, J., and Bessa, M.A., “Foundations for Computational Plasticity with Deep Learning”, PNAS, www.pnas.org/cgi/doi/10.1073/pnas.1911815116, 2019.
- Munshi, J., Ghumman, U.F., Iyer, A., Dulal, R., Chien, T., Chen, W., and Balasubramanian, G., “Effect of polydispersity on the bulk-heterojunction morphology of P3HT:PCBM solar cells”, Journal of Polymer Science, Part B: Polymer Physics, 2019. https://doi.org/10.1002/polb.24854.
- Dulal, R., Iyer, A., Ghumman, U., Munshi, J., Wang, A., Balasubramanian, G., Chen, W., Chien, T., “Elongated Nano Domains and Molecular Intermixing induced Doping in Organic Photovoltaic Active Layers with Electric Field Treatment”, ACS Applied Polymer Materials, https://doi.org/10.1021/acsapm.9b00833, 2019.
- Bostanabad, R., Liang, B., Gao, J., Liu, W. K., Cao, J., Zeng, D., Su, X., Xu, H., Li, Y. and Chen, W., “Multiscale Simulation of Fiber Composites with Spatially-Varying Uncertainties”, Uncertainty Quantification in Multiscale Materials Modeling, ed. Wang Y and McDowell, D., Elsevier S&T, 2018.
- Mansour, R., Kulachenko, A., Chen, W., Olsson, M., “Stochastic constitutive model of isotropic thin fiber networks based on Stochastic Volume Elements”, special issue on “Randomness and Uncertainty”, Materials, 12(3), 538, 2019.
- Zhao, H., Wang, Y., Lin, A., Hu, B., Yan, R., McCusker, J., Chen, W., McGuinness, D., Schadler, L., and Brinson, C.B., “NanoMine Schema: An Extensible Data Representation for Nanocomposites”, APL Materials, 6, 111108, 2018; https://doi.org/10.1063/1.
5046839 . - Munshi, J., Ghumman, U.F., Iyer, A., Dulal, R., Chen, W., Chien, T., and Balasubramanian, G., “Composition and Processing Dependent Miscibility of P3HT and PCBM in Organic Solar Cells”, Computational Materials Science, https://doi.org/10.1016/j.commatsci.2018.08.036, 2018.
- Li, X., Zhang, Y., Zhao, H., Burkhart, C., Brinson, L.C., Chen, W., “A Transfer Learning Approach for Microstructure Reconstruction and Structure-property Predictions”, Scientific Report, accepted 2018.
- Yang, Z., Li, X., Brinson, L.C., Choudhary, A.N., Chen, W., and Agrawal, A., “Microstructural Materials Design via Deep Adversarial Learning Methodology”, Journal of Mechanical Design, Special Issue on Design of Engineered Materials and Structures, doi:10.1115/1.4041371. 2018.
- Ghumman, U.F., Iyer, A., Dulal, R., Munshi, J., Wang, A., Chien, T., Balasubramanian, G., and Chen, W., “A Spectral Density Function Approach for Active Layer Design of Organic Photovoltaic Cells”, Journal of Mechanical Design, Special Issue on Design of Engineered Materials and Structures, accepted July 2018. doi:10.1115/1.4040912.
- Hansoge, N., Huang, T., Sinko, R., Xia, W., Chen, W., Keten, S., “Materials by Design for Stiff and Tough Hairy Nanoparticle Assemblies“, ACS Nano, accepted June 2018. doi: 10.1021/acsnano.8b02454.
- Bostanabad, R., Liang, B., Gao, J., Liu, W-K., Cao, J., Zeng, D., Su, X., Xu, H., Li, Y., and Chen, W. (2018). “Uncertainty Quantification in Multiscale Simulation of Woven Fiber Composites”. Computational Methods in Applied Mechanics and Engineering , 338(8), 2018.
- Bostanabad, R., Zhang, Y., Li, X., Kearney, T., Brinson, L. C., Apley, D., Wing K., and Chen, W., “Computational Microstructure Characterization and Reconstruction: Review of the State-of-the-art Techniques”, Progress in Materials Science, 95, June 2018.
- Hu, A., Li, X., Ajdari, A., Jiang, B. Burkhart, C., Chen, W., and Brinson, C., “Computational analysis of particle reinforced viscoelastic polymer nanocomposites – statistical study of representative volume element”, Journal of the Mechanics and Physics of Solids, https://doi.org/10.1016/j.jmps.2018.02.013, published online, 2018.
- Wang, Y., Zhang, Y., Zhao, H., Li, X., Huang, Y., Schadler, Linda, Chen, W., and C. Brinson, “Identifying Interphase Properties in Polymer Nanocomposites using Adaptive Optimization”, Composites Science and Technology, 2018, https://doi.org/10.1016/j.compscitech.2018.04.017.
- Chen, Z., Huang, T., Shao, Y., Li, Yang, Xu, H., Avery, K., Zeng, D., Chen, W., and X. Su, “Multiscale Finite Element Modeling of Sheet Molding Compound (SMC) Composite Structure based on Stochastic Mesostructure Reconstruction“, Composite Structures, 188, 25–38, 2018.
- Li, Yi., Chen, Z., Su, L., Chen, W., Jin, X., and Xu, H., “Stochastic Reconstruction and Microstructure Modeling of SMC Chopped Fiber Composites”, Composites Structures, accepted, 200, September 2018. https://doi.org/10.1016/j.compstruct.2018.05.079.
- Deng, J. and Chen, W., “Concurrent Topology Optimization of Multiscale Structures with Multiple Porous Materials under Random Field Loading Uncertainty”, Structural and Multidisciplinary Optimization, 56(1), 2017.
- Huang, Y., Zhao, H., Wang, Y., Ratcliff, T., Breneman, C., Brinson, L.C., Chen, W., and Schadler, L.S., “Predicting the Breakdown Strength and Lifetime of Nanocomposites using a multi-scale modeling Approach”, Journal of Applied Physics, 122, 066101, 2017
- Hassaninia, I., Bostanabad, R., Chen, W., and Mohseni, H., “Characterization of the Optical Properties of Turbid Media by Supervised Learning of Scattering Patterns”, Scientific Reports, 7, 2017.
- Lee, W-K, Yu, S., Engel, C.J., Reese, T., Rhee, D., Chen, W., and Odom, T.W., “Concurrent Design of Quasi-Random Photonic Nanostructures”, PNAS, 114(33), 2017.
- Tao, W., Liu, Z., Zhu, P., Zhu, C., Chen, W.,“Multi-scale Design of Three Dimensional Woven Composite Automobile Fender using Modified Particle Swarm Optimization Algorithm”, Composites Structures, 131, 2017.
- Bessaa, M.A., Bostanabad, R., Liu, Z., Apley, D.W., Brinson, C., Chen, W., and Liu, W-K, “A framework for data-driven analysis of materials under uncertainty: Countering the curse of dimensionality”, Computer Methods in Applied Mechanics and Engineering, 320, 633-667, 2017.
- Yu., S., Wang, C., Zhang, Y., Dong, B., Jiang, Z., Chen, X., Chen, W., and Sun, C., “Design of Non-Deterministic Quasi-random Nanophotonic Structures Using Fourier Space Representations”, Scientific Report, 7, Article number: 3752, (2017).
- Yu, S., Zhang, Y., Wang, C., Lee, W-K, Dong, B., Sun, C., Odom, T. W., and Chen, W., “Characterization and Design of Functional Quasi-Random Nanostructured Materials using Spectral Density Function”, Journal of Mechanical Design, 139(7), 2017.
- Li. W., Zhou, Q., Jiang, Z., Deng, J., and Chen, W., “Stability-Ensured Topology Optimization of Boom Structures with Volume and Stress Considerations”, Structural and Multidisciplinary Optimization, DOI 10.1007/s00158-016-1511-5, June 2016.
- Deng, J. and Chen, W., “Design for Structural Flexibility using Connected Morphable Components based Topology Optimization”, Special issue on structural topology optimization. Science China Technological Sciences, 59 (6), June 2016.
- Zhao, H., Li, X., Zhang, Yi., Schadler L.S., Chen, W., and Brinson, C., “NanoMine: A Material Genome Approach for Polymer Nanocomposites Analysis and Design”, APL Materials, 4, 053204, 2016.
- Bostanabad, R., Chen, W., Apley, D., “Characterization and Reconstruction of 3D Stochastic Microstructures via Supervised Learning”, Journal of Microscopy, DOI: 10.1111/jmi.1244, June 2016.
- Hassinger, I., Li, X., Zhao, H., Xu, H., Li, Y., Krentz, T., Huang, Y., Schadler, L., Chen, W., and I., Brinson, “Towards the Development of a Quantitative Tool for Predicting Dispersion of Nanocomposites Under Non-Equilibrium Processing Conditions“, Journal of Materials Science, 51(9), 2016.
- Zhang, Y., Zhao, H., Hassinger, I., Brinson, C., Schadler, L., and Chen, W., “Microstructure Reconstruction and Structural Equation Modeling for Computational Design of Nanodielectrics”, TMS journal of Integrating Materials and Manufacturing Innovation, DOI: 10.1186/s40192-015-0043-y. First online December 2015.
- Bostanabad R., Tuan Bui A., Wei X., Apley D., and Chen W., “Stochastic Microstructure Characterization and Reconstructionvia Supervised Learning”, Acta Materialia, DOI. 10.1016/j.actamat.2015.09.044, 2015.
- Yu, S., Zhang, Y., Wang, C., Lee, W-K, Dong, B., Sun, C., Odom, T., and Chen, W., “Characterization and Design of Functional Quasi-Random Nanostructured Materials using Spectral Density Function”, IDETC2016-60118, Proceedings of the ASME 2016 International Design Engineering Technical Conferences & Design Automation Conference, August 21-24, Charlotte, NC., 2016.
- Zhang, W., Ren, H., Wang, Z., Liu, W.K., Chen, W., Zeng, D., Su, X., and Cao, J., “An Integrated Computational Materials Engineering Method for Woven Carbon Fiber Composites Preforming Process” ESAFORM (Europe Scientific Association for Material Forming), Nantes, France, April 27-29, 2016
- Deng, J., Rorschach, K., Baker, E., Sun, C., and Chen, W., “Topology Optimization and Fabrication of Low Frequency Vibration Energy Harvesting Microdevices”, Smart Mater. Struct. 24 (2015) 025005.
- Xu, H., Liu, R., Choudhary, A., and Chen, W., “A Machine Learning-Based Design Representation Method for Designing Heterogeneous Microstructures”, Journal of Mechanical Design, 137(5), 2015.
- Yu, S., Wang, C., Sun, C., and Chen, W., “Topology Optimization for Highly-efficient Light-trapping Structure in Solar Cells”, Structural and Multidisciplinary Optimization, print online. DOI. 10.1007/s00158-014-1077-z, 2014.
- Xu, H., Li, Y., Brinson, L. C., and Chen, W., “A Descriptor-based Design Methodology for Developing Heterogeneous Microstructural Materials System”, Journal of Mechanical Design, doi:10.1115/1.4026649, 2014.
- Xu, H., Dikin, D., Burkhart, C., and Chen, W., “Descriptor-based Methodology for Statistical Characterization and 3D Reconstruction for Polymer Nanocomposites”, Computational Material Science, 85, 206-216, 2014.
- Greene, S., Li, Y., Chen. W., and Liu, W., “The Archetype-Genome Exemplar in Molecular Dynamics and Continuum Mechanics“, Computational Mechanics, 53(4), 687-737, 2014.
- Wang, C., Yu, S. Chen, W., Sun, C., “Highly Efficient Light-Trapping Structure Design Inspired By Natural Evolution”, Scientific Reports, 3: 1025, DOI: 10.1038/srep01025, 2013.
- Xu, H., Greene, S., Deng, H., Brinson, L. C., Dikin, D., Liu, W., Burkhart, C., Papakonstantopoulos, G., Poldneff, M. Chen, W., “Stochastic Reassembly Strategy for Managing Information Complexity in Heterogeneous Materials Analysis and Design”, Journal of Mechanical Design,135(10), 2013.
- Jiang, Z., Chen, W., and Burkhart, C., “Efficient 3d Porous Microstructure Reconstruction Via Gaussian Random Field and Hybrid Optimization“, Journal of Microscopy, doi: 10.1111/jmi.12077, 2013.
- Greene, M.S., Xu, H, Tang, S., Chen, W., Liu, W., “A Generalized Uncertainty Propagation Criterion from Benchmark Studies of Microstructured Material Systems”, Computer Methods in Applied Mechanics and Engineering, 254, 291-291, 2013.
- Liu, Y., Greene, M.S., Chen, W., Dikin, D., Liu, W.K., “Computational Microstructure Characterization and Reconstruction for Stochastic Multiscale Design”, Computer Aided Design, 45 (1), 65-76, 2013.
- Deng, H., Liu, Y., Gai, D. Burkhart, C., Poldneff, M., Jiang, B., Papkonstantopoulos, GJ., Dikin, D., Putz, K., Chen, W., Brinson, L.C., “Utilizing Real and Statistically Reconstructed Microstructures for the Viscoelastic Modeling of Polymer Nanocomposites”, Composite Science and Technology, 72(14), 1725-1732, 2012.
- Liu, Y., Greene, M.S., Chen, W., Dikin, D.A., and Liu, W.K., “Microstructure Reconstruction for Stochastic Multiscale Material Design”, Proceedings of the ASME 2011 International Design Engineering Technical Conferences & Computers and Information in Engineering Conference, DETC2011-48323, August 28- August 31, Washington, DC.
- Chen, S. and Chen, W., “A New Level-Set Based Approach to Shape and Topology Optimization under Geometric Uncertainty”, Structural and Multidisciplinary Optimization, 44, 1-18, April 2011.
- Greene M.S., Liu, Y., Chen, W., Liu, W.K., “Computational Uncertainty Analysis in Multiresolution Materials via Stochastic Constitutive Theory”, Journal of Computer Methods in Applied Mechanics and Engineering, 200, 309-325, January 2011.
- Chen, S., Gonella, S., Chen, W., and Liu, W.K., “A Level-Set Approach for Optimal Design of Smart Energy Harvesters”, Journal of Computer Methods in Applied Mechanics and Engineering, 199(37-40), 2532-2543, 2010.
- Chen, S., Chen, W., and Lee, S., “Level Set Based Robust Shape and Topology Optimization under Random Field Uncertainties”, Structural and Multidisciplinary Optimization, 41(4), pg 507, 2010.
- Liu, W.K., Qian, D., Gonella, S., Li, S., Chen, W., and Chirputkar, S., “Multiscale Methods for Mechanical Science of Complex Materials: Bridging from Quantum to Stochastic Multiresolution Continuum”, International Journal for Numerical Methods in Engineering,83:1039–1080, May 2010.
- Chen, W., Yin, X., Lee, S., and Liu, W. K., “A Multiscale Design Methodology for Hierarchical Systems with Random Field Uncertainty”, ASME Journal of Mechanical Design, 132, DOI: 041006, April 2010.
- Liu, W. K., Larbi, S., Tian, R., Lee, S. H., Lee, D., Yin, X., Chen, W ., Chan, S., Olson, G. B., and Lindgeen, L.-E., ” Complexity Science of Multiscale Materials via Stochastic Computations ,” International Journal for Numerical Methods in Engineering , Published online, March 2009.
- Yin, X., Lee, S., Chen, W. , Liu, W. K., Horstemeyer, M.F., “Efficient Random Field Uncertainty Propagation in Design using Multiscale Analysis” , ASME Journal of Mechanical Design , 131(2), 021006 (10 pages), 2009.
- To, A. C., Liu, W. K., Olson, G. B., Belytschko, T., Chen W. , Shephard, M., Chung, Y.-W., Ghanem, R., Voorhees, P., Seidman, D. N., Wolverton, C., Chen, J. S., Moran, B., Freeman, A. J., Tian, R., Luo, X., Lautenschlager, E., and Challoner, D., ” Materials Integrity in Microsystems: A Framework for a Petascale Predictive-Science based Multiscale Modeling and Simulation System ,” Computational Mechanics , 42(4), 485-501, September 2008.
- Yin, X., Chen, W , To, A., McVeigh, C., and Liu, W-K, “A Statistical Volume Element Method for Predicting Microstructure Constitutive Relations”, Computer Methods in Applied Mechanics and Engineering , 197(43-44), 3516-3529, 2008.